3D printing transforms
outer space and inner organs
Gears and bolts rise from the simple metal rectangle. Yet, as unassuming as it might appear, the 3D printed plate could be crucial to a successful mission to Mars and the moon.
The small pieces on the metallic surface were fused from a mix of simulated Martian dust and titanium, created layer by layer through additive manufacturing, popularly known as 3D printing. If humans set up shop on the Red Planet, they’ll be able to make repair parts or other necessities on the fly.
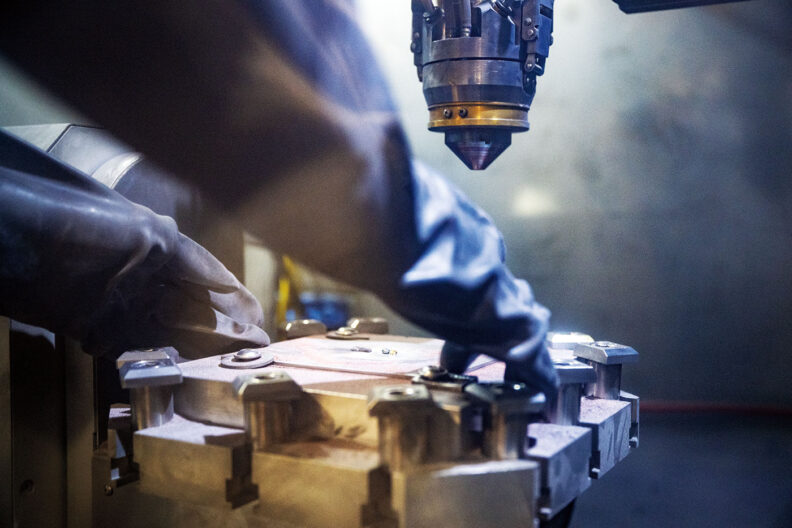
The metal plate with Martian regolith, created in a Washington State University lab, is but one way that 3D printing can rapidly transform research.
“If we’re looking at how the future is going to shift, the thing in common is 3D printing and how we can use this technology. Suppose you want to make something in seven days as opposed to seven months. In that case, 3D printing can be a solution,” says Amit Bandyopadhyay, Boeing Distinguished Professor in WSU’s School of Mechanical and Materials Engineering.
From off of Earth to inside our bodies, Bandyopadhyay and WSU colleagues are finding new uses for 3D printing. With custom machines and experimentation with different materials, WSU scientists create new things such as hip replacement implants, wearable sensors, simulated sharkskin, and parts made from extraterrestrial dust.
Additive manufacturing revolutionizes the speed and ability to make three-dimensional objects across society. Ongoing research is investigating 3D printing with living cells that could build organs and tissues for human transplants. Some companies experiment with printing food using edible materials such as chocolate and pureed vegetables, while others are creating entire buildings with huge 3D printers. In aerospace, airplane and spacecraft parts, and even most of a rocket, are 3D printed.
“You go to any industry today—space, automobiles, medical, toys—and they are innovating using additive manufacturing. Whenever you hear of manufacturing jobs returning to the US, they primarily use additive manufacturing,” Bandyopadhyay says.
The path to today’s advanced 3D printing started in a much simpler way. Bandyopadhyay and his research partner and wife, Westinghouse Distinguished Professor Susmita Bose, began at WSU in the late 1990s not long after additive manufacturing processes were commercialized.
Chuck Hull invented the first 3D printing method, stereolithography, in 1983 with a liquid photopolymer that would harden when exposed to UV light. Although his method was slow and very expensive initially, it soon paved the way for other techniques for printing in three dimensions.
One of those early developments remains the most popular 3D printing method today. Fused deposition modeling (FDM) started with a glue gun and an idea from a WSU alumnus.
In 1988, S. Scott Crump (’76 Mech. Eng.) was trying to build a toy frog for his daughter when he had an epiphany. What if he could use a glue gun–like device to print an object layer by layer? Starting with that thought, and channeling his own frustration with the slow pace of prototyping, Crump invented and patented FDM. It involves melting a thermoplastic material and extruding it through a nozzle to create layers of an object.
Crump’s first FDM machine was made from his wife’s glue gun and some spare parts from a typewriter. Crump and his wife, Lisa, went on to found Stratasys, one of the world’s leading 3D printing companies. Stratasys has been responsible for a number of breakthroughs in 3D printing, including the development of multi-material printing, which allows for the printing of objects with different materials and colors.
Crump faced some early challenges, like getting the melted plastic to stick to the platform. He solved this problem by inventing the heated platform, which keeps the plastic at a high temperature and allows it to bond with the platform.
Once the kinks were worked out, its relatively low cost and ease of use made it the most popular 3D printing method for home and some commercial use.
Other ways to print 3D objects followed FDM. One method, Selective Laser Sintering (SLS) invented by Carl Deckard in 1989, uses a laser to melt and fuse together powdered material, such as metal, plastic, or ceramic. It’s used in industries like aerospace and biomedical where high-quality and precise parts are required.
In the early days of 3D printing, Bandyopadhyay recalls the cost of an FDM machine as around $300,000. The same machine would be $500 today and sit on a desktop, he says.
The technology certainly wasn’t widespread at that early stage, but the potential was there. Bandyopadhyay holds up a white plastic gear about the size of a quarter. This likely is, he says, “the first 3D printed object made at WSU.”
The ensuing decades led to experimentation with ceramics, metal, and mixed materials in medical implants and even objects made from lunar and Martian dust.
Future missions to Mars, manned or unmanned, will require a way to repair equipment and structures. The prohibitive cost and time of transporting those materials means the parts must be made there. It costs about $54,000 for the NASA space shuttle to put just one kilogram of payload (about 2.2 pounds) into Earth’s orbit.
Bandyopadhyay, along with graduate students Ali Afrouzian and Kellen Traxel, experimented with as little as 5 percent and up to 100 percent simulated Martian regolith to make objects in the WSU lab’s large SLS printer, one of a squad of large and small printers throughout the lab.
The mixture of minerals—a close approximation of the rocky, inorganic material found on the surface of Mars—proved strong in small amounts combined with titanium, but at 100 percent it was brittle and cracked easily. Still, even materials with high Martian content would be useful in making coatings to protect equipment from rust or radiation damage, Bandyopadhyay says.
Bandyopadhyay says tests with Martian regolith are just beginning. Bose and Bandyopadhyay’s team first showed the feasibility of 3D printing parts directly from simulated crushed moon rock in 2011, in a test for NASA.
While recent work by Bandyopadhyay focuses on space, he and Bose were pioneers in using 3D printing for medical implants. It began with bones in the early 2000s.
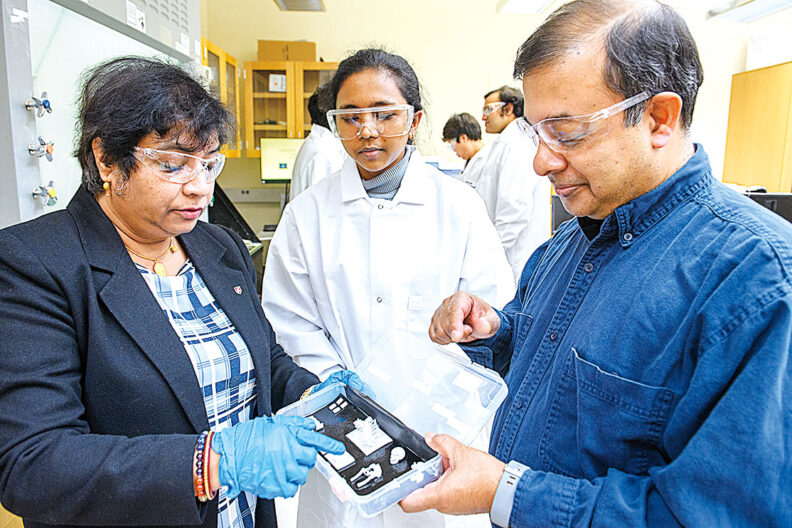
(Photo Robert Hubner)
Over 20 years back, they meticulously imaged bones as models, then used FDM to print a detailed bone model that imitates a real bone’s shape and porous architecture. Bandyopadhyay’s expertise in rapid prototyping, Bose’s materials knowledge, and support from WSU biologist Howard Hosick resulted in a novel customized bone implant that drew interest from regional medical leaders. Today, patient-matched implants via 3D printing are common worldwide.
“Not necessarily every device has to be customized. But in many cases, a customized device can improve the quality of life,” Bandyopadhyay says.
Not everyone believed in the idea, though. “A program manager told me, ‘No one will ever use 3D printed metal in a human body. We will not establish that confidence, so do something else in your life,’” Bandyopadhyay says. He and Bose ignored that comment and kept improving the techniques. Now those implants are everywhere.
Last year, as many as 150,000 3D printed metallic implants were placed just in the United States, he says. “That’s going to reach 3 to 7 million in the next five years. Once the FDA started approving devices, the companies saw the benefits.”
Meanwhile, Bose is investigating 3D printed bone-like material made mostly of chemistry-modified calcium phosphate ceramics, with additives and natural medicinal compounds to prevent infection or treat other bone disorders like osteoporosis and bone cancer, that acts as a scaffold for new tissue to grow within 3D printed interconnected porous structures.
Health care can benefit in other ways from 3D printing. Roland Chen, associate professor in mechanical engineering, sees a way to ease the expensive and painstaking process used to help people with age-related macular degeneration.
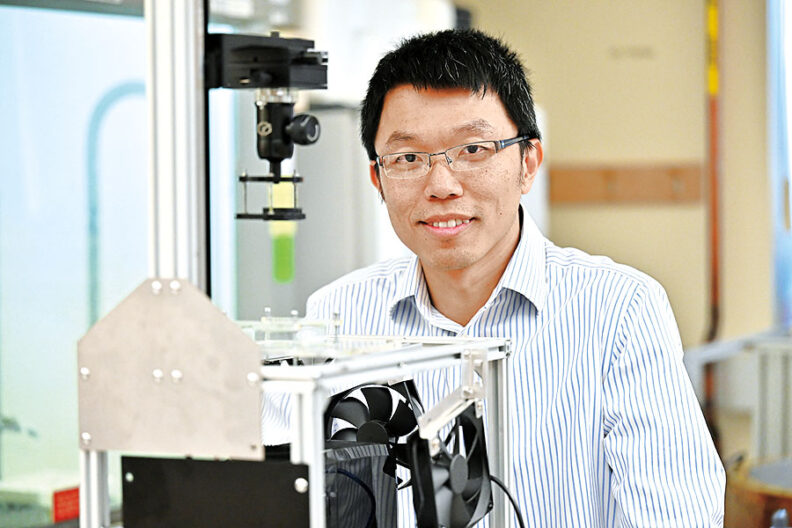
Currently, patients require a monthly booster shot in their eyeballs at $1,500 a shot. Chen’s method uses a microneedle array with controlled drug release. Using a 3D printed mold, the device made of hydrogel can also be activated by light to better control the application and removal of the array.
The microneedle, Chen says, could last many months and reduce expense and trouble for patients.
Chen and his team have also been researching 3D printed medicine, which can combine several drugs into one pill or capsule. Over 80 percent of people 65 and older take more than one medication, and reducing the number of pills could reduce adverse, and sometimes deadly, drug events.
It also would aid in correct dosages for children, Chen says. Rather than cutting pills in half or other imperfect methods, medicine could be customized to the right dose for the child’s age and body size. Smaller pills could even make it easier for kids to swallow their medicine.
Although Chen is not alone in researching 3D printed medication, he says the process is not yet scalable and will require lengthy FDA approval. However, because they are not regulated in the same way, “it could be much sooner for custom supplements and vitamins,” he says.
Biomedical research also inspires Kaiyan Qiu, Chen’s colleague in mechanical engineering. Qiu is developing presurgical organ models, wearable biosensors and electronics, biomimetic devices, and even soft robots using 3D printing.
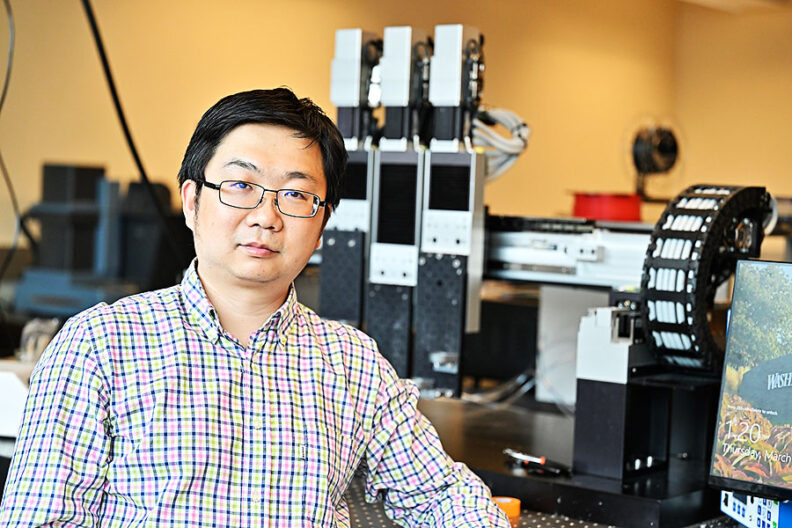
In his lab, Qiu holds up a spongy red blob that feels remarkably biological. It’s a detailed replica of a prostate that his team printed for surgeons to plan out operations before heading into the operating room.
Model organs such as the prostate and an aorta have electronic sensors built in, Qiu says, to help avoid surgically preventable errors that could lead to operation failure or death. He works with doctors and researchers at the Elson S. Floyd College of Medicine and College of Veterinary Medicine to fine-tune the organ models.
Qiu and his team have been working on a functioning cardiac model: a beating heart customized based on patient scans.
They’ve also manufactured 3D printed flexible biosensors that adhere to uneven surfaces like skin. The biosensors monitor health conditions in real time.
The Qiu lab doesn’t investigate only human organ models and sensors. WSU senior Sonja Sparks works with Qiu to perfect a simulated sharkskin. Sharks have superior drag resistance, which could benefit wet suits for the US Navy and others. Sparks, who will be a WSU doctoral student this fall, uses different materials and 3D printing approaches to fabricate and test the “sharkskin” with its small bristles.
To achieve such tiny modifications requires 3D printers with high printing resolution. In the lab, Qiu and Sparks show one of the machines with replaceable printing nozzles to achieve micrometer-size layers. One nozzle’s hole is so small that it’s invisible to the naked eye. In addition to the material deposition approach, they use another 3D printing machine to apply curing light directly on materials to form the tiny shape.
The work in Qiu’s lab represents one of the key aspects of 3D printing to Bandyopadhyay: the materials. As they try to simulate human organs or sharkskin, the researchers must try numerous combinations of materials.
“I am a material scientist who uses advanced manufacturing to make useful products,” Bandyopadhyay says. “That’s my contribution.”
The researchers use multi-material printing, such as the combination of simulated Martian regolith and titanium, to achieve the desirable properties for the job. Future projects could also leverage AI to more quickly identify material combinations.
Bandyopadhyay, Bose, and their team keep innovating not just in materials, but in machines. Even though desktop FDM 3D printers are pretty cheap, lasers are expensive to work with metal.
The WSU team has custom-built a different solution based on an old technology: welding.
Combining a $500 welding torch with a CNC, the researchers made a functional 3D printer. “You can’t do everything with the welding machine, but you can do enough,” Bandyopadhyay says.
He relishes the fun of taking a bet on 3D printing so many years ago, a bet that paid off. The same spirit of innovation keeps Qiu, Chen, Bose, Bandyopadhyay, and others thinking differently and pushing the limits of additive manufacturing.
“You have to really think upside down because you’re not taking a block and machining it. You’re staring at a platform, and you are just building the tree,” Bandyopadhyay says. “And that’s really how Mother Nature does everything, building up and not taking things out.”
Web exclusives
Make your own 3D printed WSU items with downloadable plans
More stories and videos of 3D printing research at WSU
Learn more
Infection-resistant, 3D-printed metals developed for implants (WSU Insider, November 20, 2023)
Manufacturing/3D Printing at the WSU School of Mechanical and Materials Engineering